Approach
to
New
Technologies
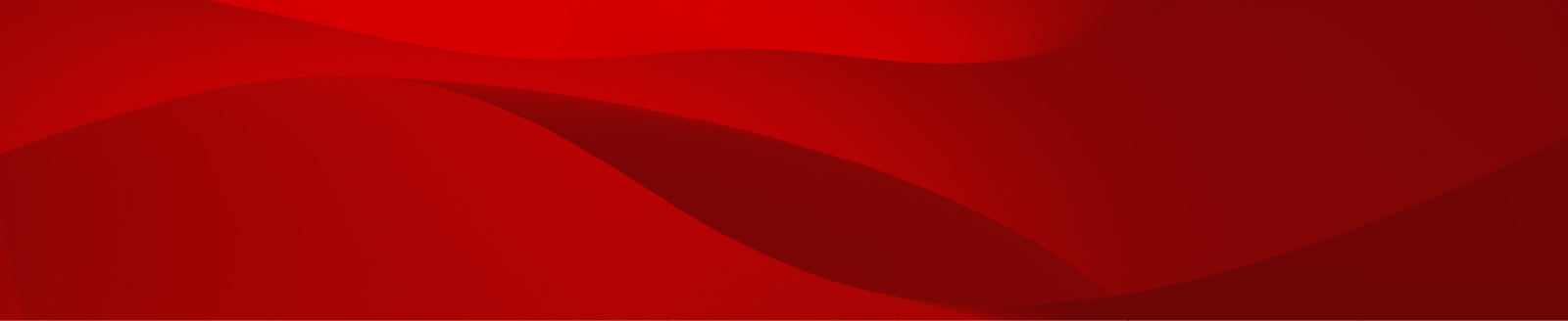
Advanced tooth surface
correction technology
for tooth surface
grinding gears.
Gears transmit power by meshing and rotating with mating gears. To ensure smooth meshing, involute curves are often used for the tooth shape. When transmitting a large amount of force, the gears deform and fail to maintain their ideal shape, resulting in partial meshing of the tooth surfaces and the loss of smooth rotation transmission. This can result in problems such as noise and tooth damage.As a countermeasure, it is common to increase the gear size or add tooth surface modification such as crowning (a slight rise of a few microns) in advance to achieve the optimum tooth surface shape after deformation. However, this is not a panacea, since larger gear sizes make the equipment heavier and larger crowning amounts at the assumed maximum torque can cause noise under light loads.Therefore, 3D tooth surface modification is advocated, such as using a flat area in the center to avoid meshing noise under light loads, and smoothly rounding the tooth surface under high loads to avoid stress concentration on the edges.
-
Without modification
-
Crowning repair
-
3D modification=
Stress Reduction
Effects of 3D tooth
surface modification
By applying 3D tooth surface modification, the size can be made smaller and lighter than conventional gears while maintaining the noise level, resulting in higher performance gears. It also contributes to CO2 reduction.
- Overall gearbox width reduction (10%)
by shortening tooth width. - Overall gearbox height reduced by 7%
due to gear diameter reduction. - Unit weight reduction due to gear
size reduction (20%). - Lower power consumption (loss reduction)
due to lower viscosity lubricating oil.
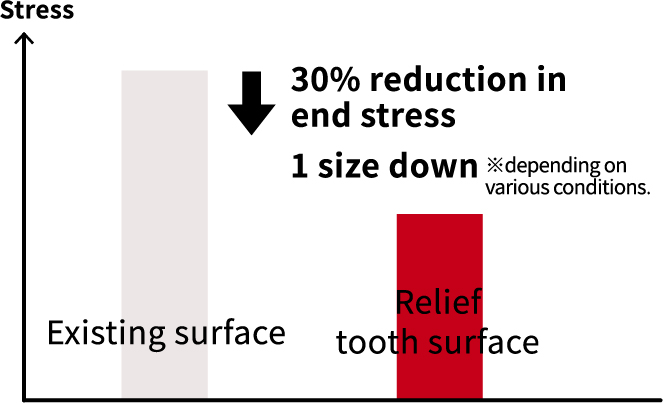

Effects of 3D tooth surface modification
based on desktop calculations
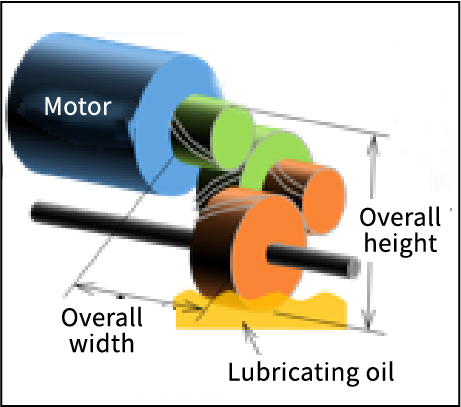
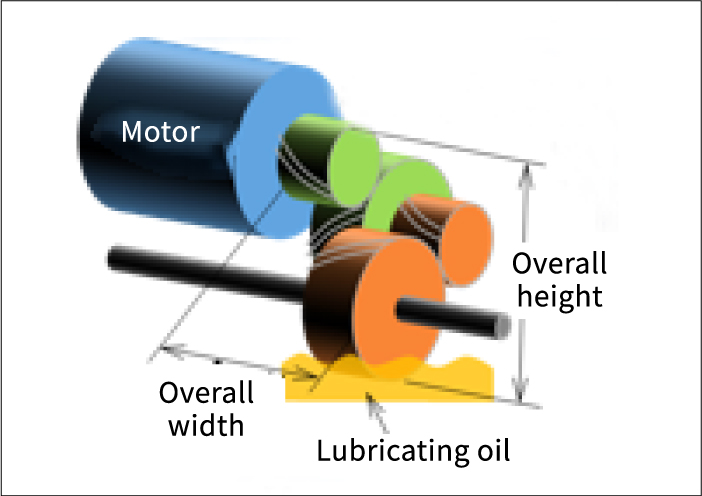
Gearbox
Simulation Technology
for Worm-like
Grinding
Wheel Gear Sharpening.
Reproduces the machined
tooth surface
on a cylindrical
gear grinder
in micron order
based on gear
origin /
tooling specifications.
Our self-developed software is packed with gear grinding technology cultivated over many years. We will partner with our customers to promote DX and bring innovation to their manufacturing.
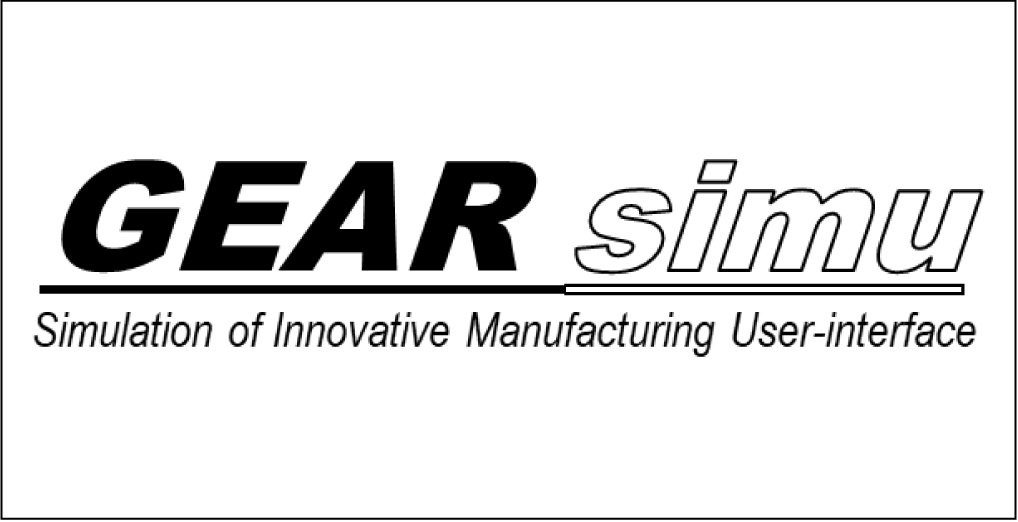
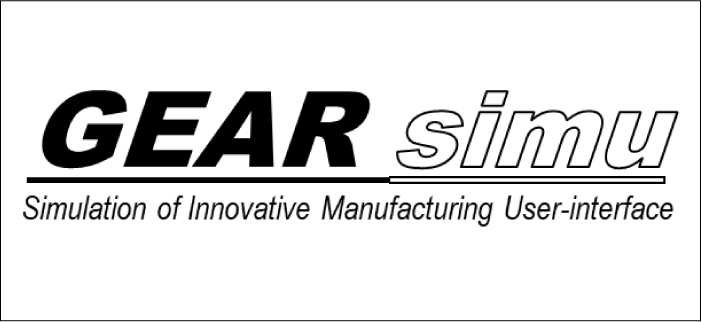
INPUT
- Workpiece
Specifications/ - Grinding
Wheel
Specifications/ - Dresser
Specifications/ - Dressing
Conditions/ - Machining
Conditions
Dress Simulation
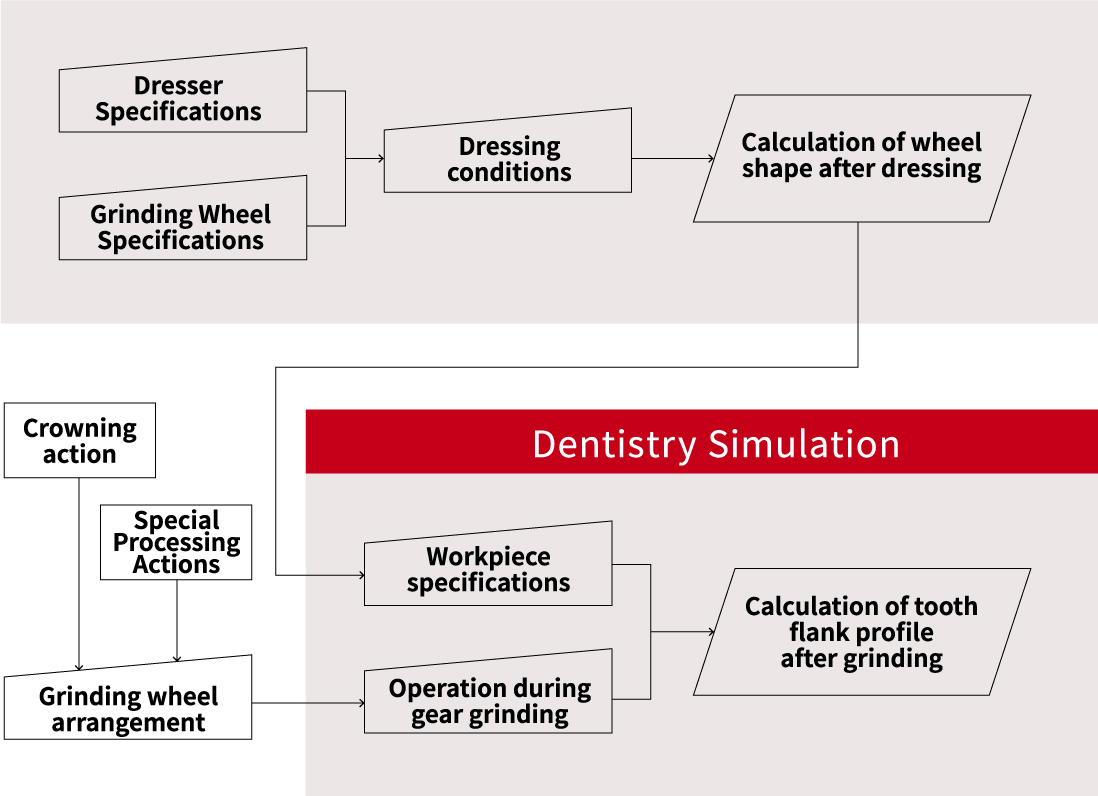
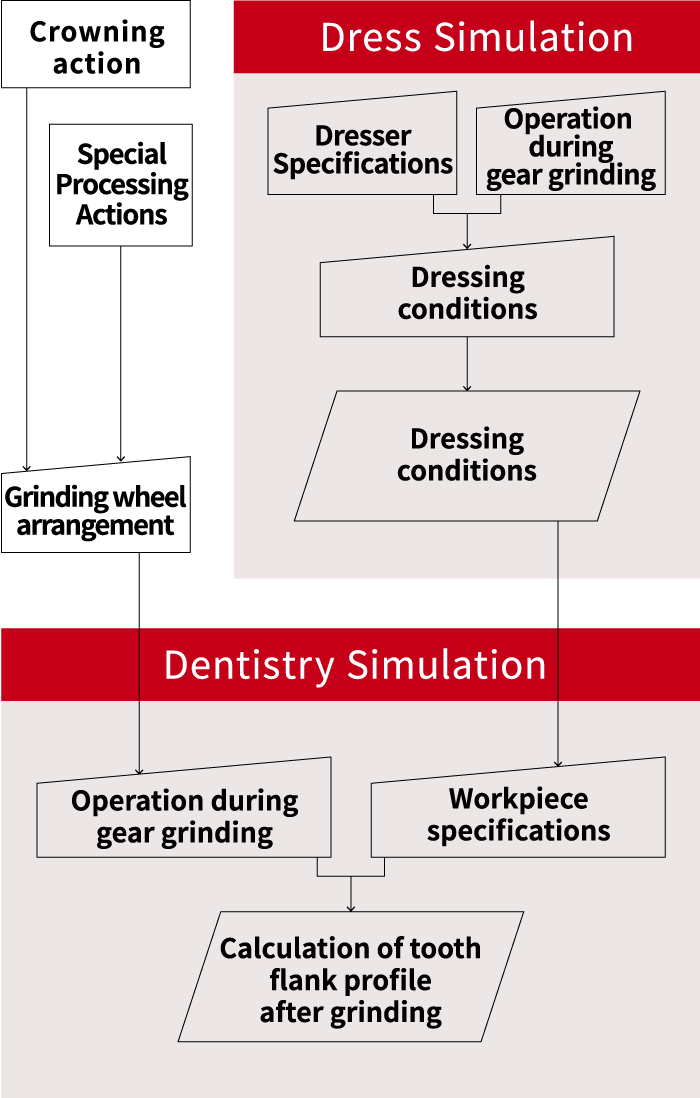
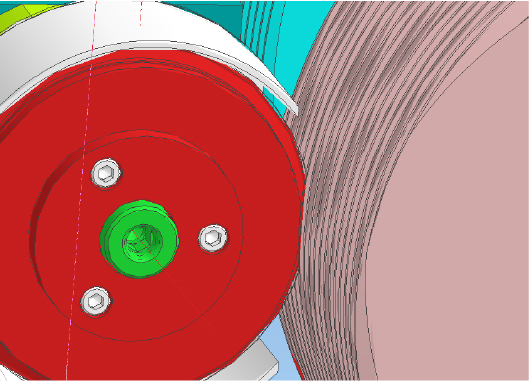
Image of Dress Simulation
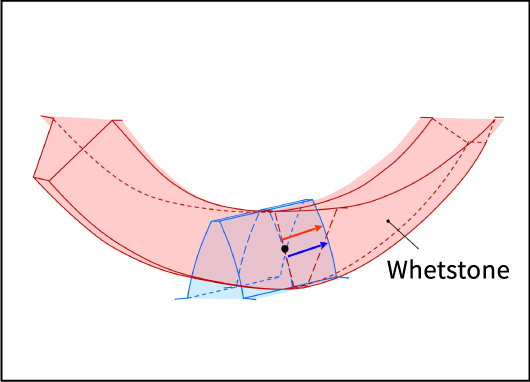
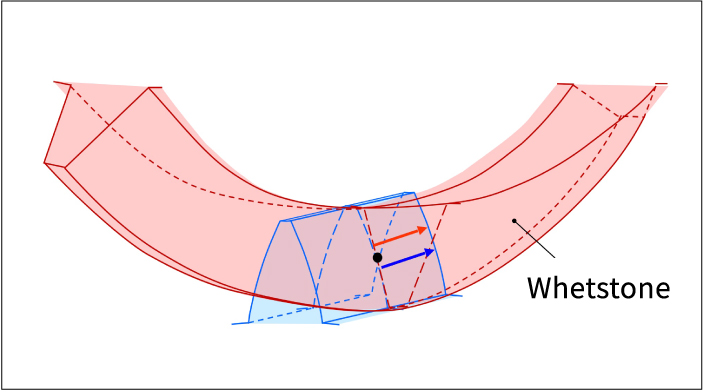
Image of
Dental Research Simulation
OUTPUT
- Grinding
wheel shape/ - Tooth
surface shape/ - Where to use
boulders
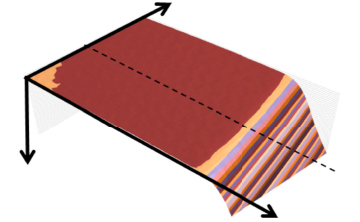
Shape of tooth flank
after machining
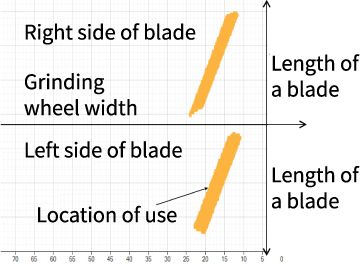
Where to use boulders
Effects of “GEAR simu”
It can solve issues with
tooth grinding processing.
1Confirmation of
processing shape.
We can also accommodate special processing operations. This can lead to a reduction in trial processing man-hours and a shortened lead time.
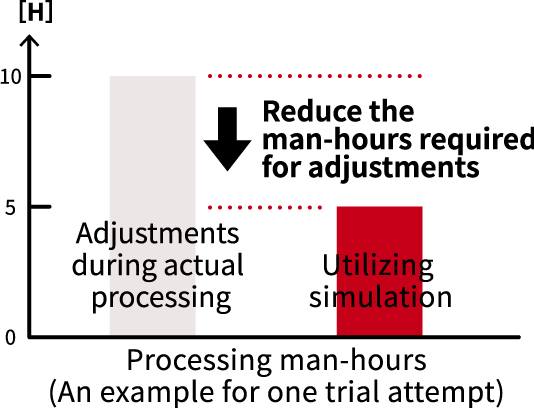
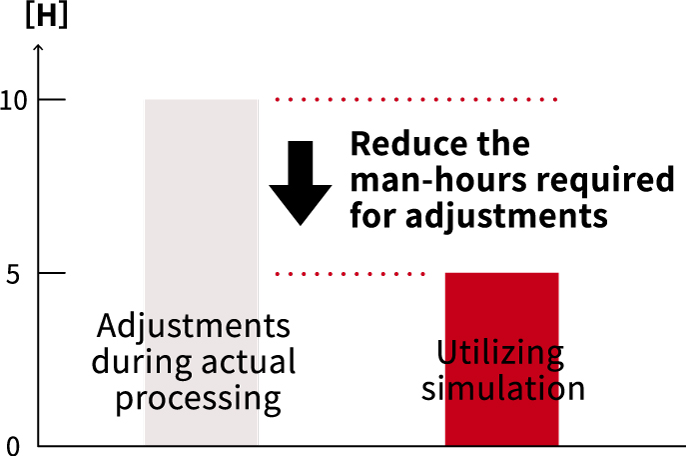
Processing man-hours
(An example for one trial attempt)
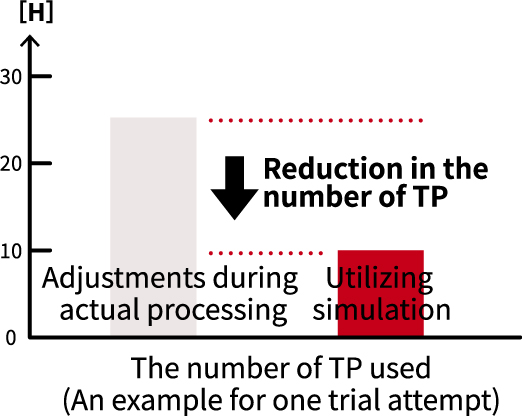
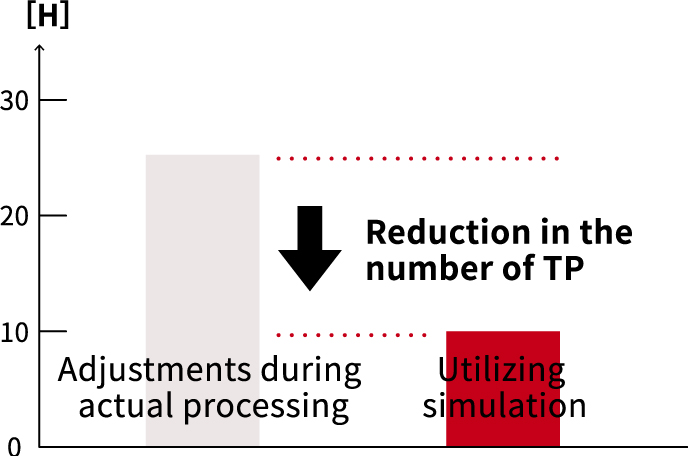
The number of TP used
(An example for one trial attempt)
2Positioning of the
grinding stone.
It is possible to optimize shift conditions and improve dress intervals.